Vibration isolators for pipe systems are essential for maintaining the structural integrity and minimizing noise and vibration in industrial and commercial settings. Choosing the right vibration isolators for pipe systems is crucial to ensuring the overall safety and performance of the system. Different types of vibration isolators are available, seismic isolators each designed to suit specific applications and environments. In this article, we will explore the factors to consider when choosing vibration isolators for pipe systems and the importance of selecting the right isolators for optimal performance.
When choosing the right vibration isolators for pipe systems, it is important to consider factors such as the type seismic base isolators of pipe material, the diameter and length of the pipes, the flow rate of the media being transported, and the operating temperature and pressure. Additionally, the surrounding environment, such as the presence of heavy machinery or other sources of vibration, should also be taken into account. There are various types of vibration isolators available, including rubber, neoprene, and spring isolators, each with their own advantages and limitations. Rubber and neoprene isolators are effective for absorbing high-frequency vibrations, while spring isolators are better suited for low-frequency vibrations. The selection of the appropriate isolator type will depend on the specific requirements of the pipe system. It is also essential to ensure that the chosen vibration isolators comply with industry standards and regulations, as well as the specific requirements of the application. Proper installation and maintenance of the isolators are crucial for their effectiveness in reducing vibration and noise in the pipe system. In summary, choosing the right vibration isolators for pipe systems involves careful consideration of various factors such as pipe specifications, operating conditions, environmental factors, and compliance with standards. By selecting the most suitable isolators and ensuring proper installation and maintenance, the integrity and efficiency of the pipe system can be safeguarded.
When choosing the right vibration isolators for pipe systems, it is crucial to consider the specific requirements of the application. Factors to consider include the type of pipe material, diameter, length, flow rate, operating temperature, seismic isolation structure pressure, and surrounding environment. Various types of vibration isolators such as rubber, neoprene, and spring isolators are available, each with distinct advantages based on the frequency of vibrations they are designed to absorb. Compliance with industry standards and regulations, as well as proper installation and maintenance, are essential for the effective reduction of vibration and noise in the pipe system. Overall, selecting the most suitable isolators and ensuring their appropriate installation and maintenance is vital for preserving the integrity and efficiency of the pipe system.
The Importance of Vibration Isolators for Pipe Systems

Vibration isolators for pipe systems are essential for maintaining the integrity and functionality of the system. These isolators are designed to absorb and minimize the transmission of vibration and noise within the piping network. By reducing the effects of vibration, isolators help prevent damage to the piping, as well as connected equipment and structures. They also contribute to a safer and more comfortable working environment by reducing noise levels and mitigating the potential for fatigue and stress on the system components. Overall, vibration isolators play a crucial role in ensuring the reliability and longevity of pipe systems in various industrial, commercial, and residential applications.
Choosing the Right Vibration Isolators for Your Piping
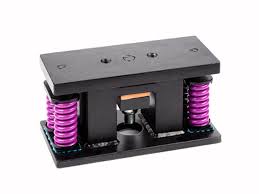
When selecting vibration isolators for piping, it's important to consider factors such as the type and frequency of vibration, the weight and size of the piping system, and the location and environment in which the piping will be installed. Different types of isolators, such as spring, rubber, or neoprene, may be more or less suitable for specific applications. It's also crucial to ensure that the isolators are properly sized and installed to effectively reduce vibration and protect the piping system from potential damage. Consulting with a professional engineer or vibration isolation expert can help in determining the most suitable isolators for a specific piping system.
Common Misconceptions About Vibration Isolators for Pipes
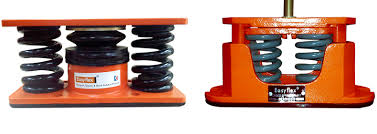
Some common misconceptions about vibration isolators for pipes include the belief that they are unnecessary for small or lightweight pipes. In reality, even smaller pipes can generate significant vibrations that can lead to issues such as noise, structural damage, and premature equipment failure. Additionally, some may believe that vibration isolators are only needed for high-pressure or high-temperature piping systems, when in fact, any system that generates vibrations can benefit from the use of isolators. Another misconception is that vibration isolators are a one-size-fits-all solution. In reality, selecting the right isolator requires consideration of factors such as pipe size, material, and operating conditions to ensure effective vibration control.
Effective Ways to Install Vibration Isolators for Pipe Systems
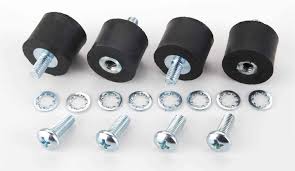
When installing vibration isolators for pipe systems, it is important to consider the following effective methods: 1. Properly selecting isolators: Choose isolators that are suitable for the specific requirements of the pipe system, including the size and weight of the piping, as well as the level and frequency of vibration expected. 2. Ensuring correct placement: Install isolators at key points along the pipe system where vibrations are most likely to occur, such as at connections, corners, and near heavy machinery. 3. Providing adequate support: Ensure that the pipe system is adequately supported to prevent excessive movement and stress on the isolators. 4. Using appropriate fasteners: Use appropriate fasteners, such as heavy-duty bolts and brackets, to securely attach the isolators to the pipe system and the surrounding structure. 5. Conducting regular maintenance: Inspect the isolators regularly to ensure that they remain in good working condition and replace any worn or damaged isolators as needed. By following these effective methods, vibration isolators can be installed to effectively minimize the transmission of vibrations in pipe systems, leading to improved performance and reduced maintenance needs.
Maximizing the Lifespan of Your Piping with Vibration Isolators
Vibration isolators play a crucial role in maximizing the lifespan of piping systems by reducing the effects of vibration, which can lead to fatigue and failure over time. These isolators can help to protect piping from damage caused by excessive movement, which can occur due to factors such as machinery operation, environmental conditions, or changes in flow rates within the system. By effectively isolating vibrations, these components can help to prolong the life of piping and prevent costly repairs or replacements. Proper selection and installation of vibration isolators are essential for ensuring the long-term performance and durability of piping systems. Regular maintenance and inspection of isolators are also important for identifying and addressing any issues that may arise over time. Overall, incorporating vibration isolators into piping design and maintenance practices can contribute to maximizing the lifespan of piping systems.
The Role of Vibration Isolators in Preventing Pipe Failure
Vibration isolators play a critical role in preventing pipe failure by absorbing and dampening the vibrations that can occur during the operation of piping systems. These isolators are designed to minimize the transfer of vibration from the surrounding environment to the pipe, reducing the risk of fatigue and stress on the piping system. By installing vibration isolators at strategic points along the pipe network, potential damage from vibration-induced fatigue, resonance, and harmonic oscillation can be mitigated. This helps to extend the lifespan of the pipes and avoid costly repairs or replacements due to premature failure. In addition, vibration isolators can also minimize the transmission of noise and vibration to nearby structures, improving the overall environmental impact and reducing potential health and safety concerns. Overall, the role of vibration isolators in preventing pipe failure is essential for maintaining the integrity and longevity of piping systems in various industrial, commercial, and residential applications.
Understanding the Different Types of Vibration Isolators for Pipes
Vibration isolators for pipes come in various types, including spring isolators, neoprene isolators, and rubber isolators. Spring isolators are typically used for large, heavy equipment and provide high vibration isolation efficiency. Neoprene isolators are suitable for light to moderate loads and offer good resistance to oils and chemicals. Rubber isolators are commonly used for smaller equipment and provide good vibration isolation and noise reduction. Understanding the different types of vibration isolators for pipes is crucial in choosing the right solution for specific equipment and environmental conditions.
Key Factors to Consider When Selecting Vibration Isolators for Pipes
1. Load Capacity: Ensure that the vibration isolator can support the weight and pressure of the piping system. 2. Vibration Frequency: Select vibration isolators that can effectively dampen the specific frequency of vibrations present in the system. 3. Environmental Conditions: Consider factors such as temperature, humidity, and exposure to chemicals when choosing vibration isolators to ensure they are suitable for the environment. 4. Installation Method: Determine the most appropriate installation method for the vibration isolators based on the layout and accessibility of the piping system. 5. Maintenance Requirements: Assess the maintenance needs of different types of vibration isolators and choose ones that align with the available resources and schedule. 6. Cost: Evaluate the upfront and long-term costs of different vibration isolator options, considering factors such as initial purchase price and expected lifespan.
In conclusion, selecting the appropriate vibration isolators for pipe systems is crucial in ensuring the longevity and efficiency of the entire system. By considering factors such as load capacity, vibration frequency, and environmental conditions, one can effectively mitigate the effects of vibration and ensure the smooth operation of the pipes. Therefore, it is essential to carefully choose the right vibration isolators for pipe systems to maintain their integrity and functionality in the long run.
multi axis capability isolator
See also
https://www.globalindustrial.com/t/material-handling/vibration-dampers/vibration-isolators https://www.paulstra-industry.com/en/products/vibration-isolation https://www.techproducts.com/